CASMPD: Integrated Computer-Aided Solvent, Material & Process Design
Our group has many years of research experience in developing CASMPD methods for integrated solvent and process design tasks [1]. This research line was continued in recent years with special focus on the integrated design of ionic liquids (ILs) and absorption processes as well as integrated design of metal-organic frameworks (MOFs) and adsorption processes. The most important research aspects were: a) design of IL for CO2 capture, b) design of IL-based phase change materials (PCM) for efficient thermal storage, c) design of MOF for hydrogen storage and gas separation. In order to accurately predict solvent and material properties and more efficiently solve the design problem, machine learning and surrogate modeling approaches have been appropriately employed.
Although ILs were considered and investigated already as promising solvents for CO2 capture by several groups, e.g. [2], systematic IL selection and molecular design studies are still scarce. In particular, to the best of our knowledge, so far there has been no rate-based CO2-in-IL absorption model for process and molecular design available. The reason for the lack of rate-based approaches is that, if used in a design task, they lead to complex optimization problems. To fill this gap, recently the PSE group have built a machine learning-based group contribution (GC) model to directly predict the CO2 solubility in various ILs at different conditions [3]. This surrogate model was used to substitute the traditional thermodynamic model, thereby making it possible to identify the global optimum of the integrated IL-process design problem (Fig. 1). It was found that the optimal IL-based CO2 absorption process can potentially save ca. 15% of the overall cost compared to the industrial Selexol process [4].
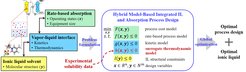
The CASMPD methodology was also applied for IL-based PCM design where the optimally designed material shows a more than 30% higher heat storage capacity than the traditionally used PCM, paraffin wax [5].
MOFs have attracted considerable attention in gas storage and separation due to their structural diversity, high porosity, and tailorable functionality. An integrated MOF and pressure/vacuum swing adsorption (P/VSA) process design framework was proposed by our group [6]. As indicated in Fig. 2, it consists of two steps: MOF descriptor optimization and MOF matching. In the first step, MOFs are represented as a large set of chemical and geometric descriptors from which the most influential ones are selected and treated as design variables. The valid design space of the selected descriptors is confined using a tailored classifier model and logic constraints. Based on collected adsorption isotherms of 471 different MOFs, data-driven isotherm models are developed. Combining the design space, isotherms, and P/VSA process models, an integrated MOF and P/VSA process design problem is formulated. MOF descriptors and process operating conditions are optimized to maximize the process performance. The obtained optimal descriptors and isotherms can be used to guide the discovery of high-performance materials in a subsequent MOF matching step. This is the subject of our current research activities in this project.
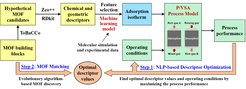
Publications
[1] Zhou, T., McBride, K., Linke, S., Song, Z., & Sundmacher, K. (2020). Computer-aided solvent selection and design for efficient chemical processes. Current Opinion in Chemical Engineering, 27, 35-44.
[2] Florin, N., Buchard, A., Hallett, J., Galindo, A., Jackson, G., Adjiman, C.S., Williams, C.K., Shah, N., & Fennell, P. (2010). An overview of CO2 capture technologies. Energy & Environmental Science, 3(11), 1645-1669.
[3] Song, Z., Shi, H., Zhang, X., & Zhou, T. (2020). Prediction of CO2 solubility in ionic liquids using machine learning methods. Chemical Engineering Science, 223, 115752.
[4] Zhang, X., Ding, X., Song, Z., Zhou, T., & Sundmacher, K. (2021). Integrated ionic liquid and rate-based absorption process design for gas separation: global optimization using hybrid models. AIChE Journal, 67(10), e17340.
[5] Shi, H., Zhang, X., Sundmacher, K., & Zhou, T. (2021). Model-based optimal design of phase change ionic liquids for efficient thermal energy storage. Green Energy & Environment, 6, 392-404.
[6] Zhang, X., Zhou, T., & Sundmacher, K. (2022). Integrated MOF and P/VSA process design: Descriptor optimization. AIChE Journal, doi: 10.1002/aic.17524.