InPROMPT: Integrated Chemical Processes with Thermomorphic Multicomponent Phase Systems
The Collaborative Research Center (CRC/TR 63) InPROMPT with our partners from TU Berlin, TU Dortmund and OVGU focuses on the sustainable processing of renewable oleochemical substances by use of homogeneous catalysts, which are recovered with the help of novel, temperature-switchable multicomponent solvent systems [1]. The PSE group contributes to all hierarchical levels of process synthesis – from phase system selection to the experimental validation (Fig. 1) – while simultaneously adhering to the principles of Green Chemistry.
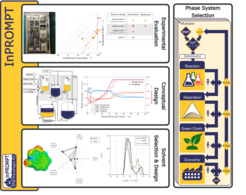
As a foundation for the conceptual design, a systematic framework for the design of solvent systems was proposed [2]. The algorithm consists of an iterative process in which a reaction system is designed by continuously adding additional degrees of freedom in the form of auxiliary substances like solvents and surfactants if the predefined process requirements are missed. To supplement the phase system selection, a solvent screening methodology was developed for the design of Thermomorphic Multiphase Systems (TMS) using COSMO-RS for the thermodynamic properties and QSAR models for the environmental properties. This led to the identification of replacement solvents for the developmental toxic dimethylformamide [3]. Working collaboratively with the PSD group (headed by Prof. Kienle), an integrated solvent and process design approach based on 𝜎-moments was developed [4, 5]. Moreover, the estimation of environmental properties, such as bioaccumulation, was achieved by using Graphical Neural Networks (GNN) for linking the molecular structures to the properties of the solvent molecules [6]. Furthermore, by applying the EPF methodology in combination with the flux profile analysis, optimal reactor networks and operating conditions for the hydroformylation reaction were identified. Two reactor tandems comprising a repeatedly operated semi-batch reactor and a helically coiled tubular reactor, respectively followed by a continuously stirred tank reactor (CSTR), were constructed and operated continuously in a miniplant for more than 500 hours [7]. Compared to a single CSTR, the conversion and target product yields were enhanced by up to 25% [7, 8, 9, 10, 11, 12].
Publications
[1] https://www.inprompt.tu-berlin.de/
[2] Kraume, M., Enders, S., Drews, A., Schomäcker, R., Engell, S. & Sundmacher, K. (Eds.) (2021) Integrated Chemical Processes in Liquid Multiphase Systems: From Chemical Reaction to Process Design and Operation, De Gruyter, Berlin, ISBN: 978-3-11-070943-8, in press.
[3] Linke, S., McBride, K., & Sundmacher, K. (2020). Systematic Green Solvent Selection for the Hydroformylation of Long - Chain Alkenes. ACS Sustainable Chemistry & Engineering, 8 (29), 10795–10811. doi: 10.1021/acssuschemeng.0c02611.
[4] Keßler, T., Kunde, C., Linke, S., McBride, K., Sundmacher, K., & Kienle, A. (2019). Systematic Selection of Green Solvents and Process Optimization for the Hydroformylation of Long-Chain Olefines. Processes, 7 (12): 882. doi: 10.3390/pr7120882.
[5] Keßler, T., Kunde, C., Linke, S., Sundmacher, K., Kienle, A. (2021). Integrated Computer-Aided Molecular and Process Design: Green Solvents for the Hydroformylation of Long-Chain Olefines. Chemical Engineering Science, accepted, preprint: https://zenodo.org/record/5139524
[6] Sanchez Medina, E. I., Linke, S., & Sundmacher, K. (2021). Prediction of Bioconcentration Factors (BCF) using Graph Neural Networks. In: 31st European Symposium on Computer Aided Process Engineering: Computer Aided Chemical Engineering, 991–997. ISBN: 9780323885065. doi: 10.1016/B978-0-323-88506-5.50153-4.
[7] Jokiel, M. (2020). Optimale Reaktionsführung durch Reaktor-Tandems am Beispiel der Hydroformylierung von 1-Dodecen. PhD Thesis, Magdeburg: Otto-von-Guericke-Universität
[8] Jokiel, M., Kaiser, N. M., Kováts, P., Mansour, M., Zähringer, K., Nigam, K. D. P., & Sundmacher, K. (2019). Helically coiled segmented flow tubular reactor for the hydroformylation of long-chain olefins in a thermomorphic multiphase system. Chemical Engineering Journal (ISCRE 25 Special Issue), 377: 120060. doi: 10.1016/j.cej.2018.09.221.
[9] Jokiel, M., Rätze, K., Kaiser, N. M., Künnemann, K., Hollenbeck, J.-P., Dreimann, J. M., Vogt, D., & Sundmacher, K. (2019). Miniplant-Scale Evaluation of a Semibatch-Continuous Tandem Reactor System for the Hydroformylation of Long-Chain Olefins. Industrial and Engineering Chemistry Research, 58 (7), 2471–2480. doi: 10.1021/acs.iecr.8b03874.
[10] Rätze, K., Jokiel, M., Kaiser, N. M., & Sundmacher, K. (2019). Cyclic Operation of a Semi-Batch Reactor for the Hydroformylation of Long-Chain Olefins and Integration in a Continuous Production Process. Chemical Engineering Journal (ISCRE 25 Special Issue), 377: 120453. doi: 10.1016/j.cej.2018.11.151.
[11] Jokiel, M. & Sundmacher, K. (2018). Spezielle labortechnische Reaktoren: Wendelrohrreaktor. In: Reschetilowski, W. (Eds.) Handbuch Chemische Reaktoren - Grundlagen und Anwendungen der Chemischen Reaktionstechnik. Springer-Verlag GmbH Deutschland. ISBN: 978-3-662-56444-8. doi: 10.1007/978-3-662-56444-8_46-1.
[12] Kaiser, N.M. (2018) From Reaction Kinetics to the Miniplant: Dynamic Optimization-based Reactor Synthesis and Design under Uncertainty for Liquid Multiphase Processes. PhD Thesis, Otto-von-Guericke-Universität, Magdeburg.