Dynamics of Multichamber Granulation Processes
Introduction
Fluidized bed spray granulation is an important class of particulate processes. Focus in this project is on multichamber processes as depicted in Fig. 1. In this configuration the granulation chamber is divided into serveral sections, each can have its own operating conditions and own external feed streams either by injecting some liquid suspension, or adding some seeds generated for example by an external sieve mill loop. Therefore, different subprocesses such as layering granulation, coating, cooling or drying can be realized in the different sections of the granulation chamber. Although this kind of processes is frequently used in industry, a fundamental understanding of its dynamic behavior is lacking. This, however, is a necessary prerequisite for stable production of particles with tailor-made properties. For this purpose, the project aims at the development of predictive dynamic models. Important issues which are addressed are zone formation in the different chambers, the effect of granulation and drying kinetics on product properties, axial transport across the weirs and dynamic stability of continuous operated FBLGs. The project is accompanied by experimental studies. In cooperation with the project “Control of particulate processes” different types of closed loop controllers are designed and applied to speed up the experiments and enhance the reproducibility. The project is embedded in the DFG priority program SPP 1679 on dynamic simulation of coupled particle processes. Project partners are Prof. Heinrich from Hamburg University of Technology, Prof. Tsotsas from Otto von Guericke University Magdeburg, and Prof. Bück from Friedrich Alexander University Erlangen-Nuremberg.
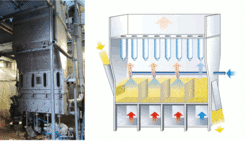
Figure 1: Multichamber fluidized bed granulation process
Results
Open and closed loop dynamics of continuous fluidized bed spray granulation (FBSG) with internal and external product classification is studied theoretically and experimentally. Experiments with internal product classification were conducted by our cooperation partners at OVGU. Experiments with external product classification were conducted in collaboration with the group led by Prof. Heinrich in Hamburg. Initially the project focused on open loop instability. This is a characteristic feature of many particulate processes. It leads to a cyclic change of product properties and is therefore not desirable. For processes with internal product classification a rigorous theoretical stability and bifurcation analysis was provided in [1]. Compared to previous work by [2] an additional stability boundary was identified With this finding, for the first time a consistent explanation of experimental observations in [3] was possible.
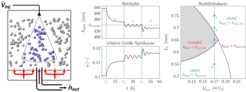
Figure 2: Left: scheme of FBSG with internal prodcut classification. Right: Dynamic simulation and stability map of FBSG with internal product classification.
For processes with external product classification our previous analysis in [4] was complemented by recent results in [5]. The focus was on the influence of zone formation within the fluidized bed on process stability and a quantitative relation to different process configurations commonly used in practice. For experimental validation a new plant was started up in Hamburg during the reporting period. Theoretical insights obtained by the PSD group guided the way towards feasible plant operation which is limited by many practical constraints arising mainly from the product withdrawal, grinding and recycling of oversized particles to provide new nuclei to the granulation chamber (see Fig. 3). It turned out that the model of the milling process had to be refined [6] to obtain a quantitative agreement between model predictions and measurements. Recent work has been concerned with an extension of the population balance modeling approach for granulation processes. Besides particle size, the influence of thermal conditions on particle porosity, temperature and humidity is also taken into account [7]. An additional area of focus is the modeling of continuous agglomeration processes in fluidized beds [8]. This is a rather new type of process which is also of great interest for industry.
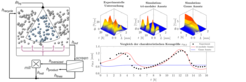
Figure 3: Left: scheme of FBSG with external prodcut classification. Right: comparison between theoretical and experimental results for different mill models.
Future Directions
Based on the established dynamic models new concepts of process and product design for multichamber FBSG will be derived.
Cooperation Partners
- Prof. S. Heinrich: Institute of Solids Process Engineering and Particle Technology, TU Hamburg.
- Prof. A. Bück: Institute of Particle Technology (LFG), FAU Erlangen-Nuremberg.
- Prof. Tsotsas: Thermal Process Engineering, OVGU Magdeburg.
This project is embedded in the national priority program SPP 1679 with funding from the DFG.
Publications
[1] C. Neugebauer, S. Palis, A. Bück, E. Tsotsas, S. Heinrich, and A. Kienle. A dynamic two zone model of continuous fluidized bed layering granulation with internal product classification. Particuology, 31:8–14, 2017.
[2] A. Vreman, C. van Lare, and M. Hounslow. A basic population balance model for fluidized bed spray granulation. Chem. Eng. Sci., 64:4389–4398, 2009.
[3] M. Schmidt, A. Bück, and E. Tsotsas. Experimental investigation of process stability of continuous spray fluidized bed layering granulation with internal separation. Chem. Eng. Sci., 126:55–66, 2015.
[4] C. Dreyschultze, C. Neugebauer, S. Palis, A. Bück, E. Tsotsas, S. Heinrich, and A. Kienle. Influence of zone formation on stability of continuous fluidized bed spray granulation with external product classification. Particuology, 23:1–7, 2015.
[5] A. Bück, C. Neugebauer, K. Meyer, S. Palis, E. Diez, A. Kienle, S. Heinrich, and E. Tsotsas. Influence of operation parameters on process stability in continuous fluidized bed layering with external classification. Powder Technol., 300:37–45, 2016.
[6] C. Neugebauer, S. Palis, A. Bück, E. Diez, S. Heinrich, E. Tsotsas, and A. Kienle. Influence of mill characteristics on stability of continuous layering granulation with external product classification. In Computer Aided Chem. Eng., 38:1275-1280, 2016.
[7] C. Neugebauer, A. Bück, S. Palis, L. Mielke, E. Tsotsas, and A. Kienle. Influence of thermal conditions on particle properties in fluidized bed granulation, 2018. Paper presented at PBM 2018 in Ghent/Belgium.
[8] I. Golovin, G. Strenzke, M. Wegner, S. Palis, A. Bück, A. Kienle, and E. Tsotsas. Parameter identification for continuous fluidized bed spray agglomeration, 2018. Paper presented at PBM 2018 in Ghent/Belgium.