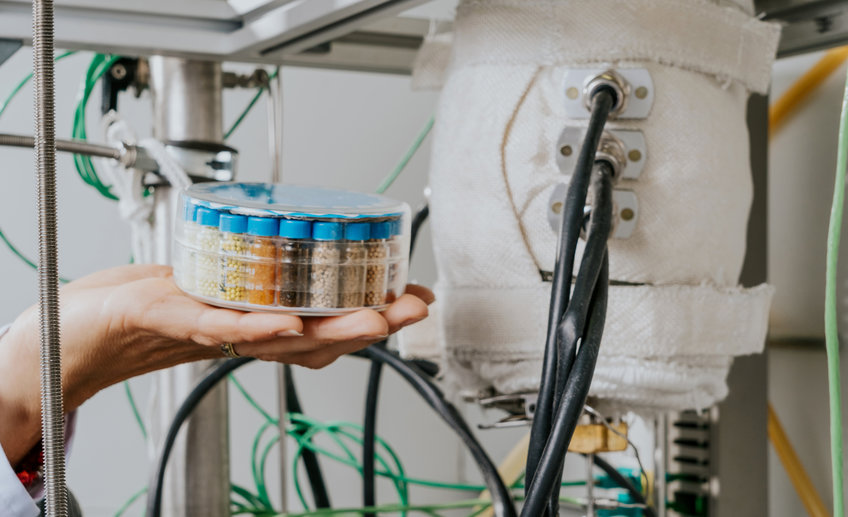
Dynamic operation
The effective control and use of dynamic reactor operation is essential to enhance the desired performance parameters. Dynamic operation can be either systemic, i.e. catalyst deactivation, or forced, modulation of inlet parameters. With the application of suitable methodologies, it is possible to determine dynamic operating parameters that enhance a process compared to their steady state operation. Further, dynamic operation of multifunctional reactors can be used to reduce downtimes compared to conventional reactor concepts.
Nonlinear Frequency Response Method
In chemical processes it is usually desired to prevent dynamic behavior of the system. Even though, it was proven that suitable dynamic parameters result in beneficial performance. The application of theoretical results of forced periodic operation has been limited, because of inaccurate predictability.
A relatively new and fast method to evaluate dynamic reactor operation is the nonlinear frequency response (NFR). This method, based on control theory, predicts the output of forced periodically operating single and multiple input parameters (Figure 1), such as inlet concentration, total flow and inlet temperature. In a collaboration with the University of Belgrade sinusoidal changes and more general waveforms of these inputs are being validated.
![Figure 1: Schematic illustration inputs modulating resulting in a fluctuating output, which is beneficial when the time-average is higher compared to the steady state case for the product.[Felischak, M., Kaps, L., Hamel, C., Nikolic, D., Petkovska, M., & Seidel-Morgenstern, A. (2021). Analysis and experimental demonstration of forced periodic operation of an adiabatic stirred tank reactor: Simultaneous modulation of inlet concentration and total flow-rate. Chemical Engineering Journal, 128197.]](/4224743/original-1636969253.jpg?t=eyJ3aWR0aCI6MjQ2LCJvYmpfaWQiOjQyMjQ3NDN9--68a362bf3f458f4861b9e70d36b896ac93b94db5)
[Felischak, M., Kaps, L., Hamel, C., Nikolic, D., Petkovska, M., & Seidel-Morgenstern, A. (2021). Analysis and experimental demonstration of forced periodic operation of an adiabatic stirred tank reactor: Simultaneous modulation of inlet concentration and total flow-rate. Chemical Engineering Journal, 128197.]
The NFR method is based on the concept of higher order frequency response functions (FRFs) and is applicable for weakly nonlinear systems. Frequency response of a weakly nonlinear system, in addition to the basic harmonic, contains a non-periodic (DC) term and, theoretically, an infinite sequence of higher harmonics. The DC component of the output is responsible for the average performance of the periodically operated reactor, and its sign and value define whether, and to which extent, the periodic operation leads to process improvement.
Forced Simultaneous Modulation of Multiple Reactor Inlet Parameter
As an example, the hydrolysis of acetic anhydride in an adiabatic CSTR has been chosen. In order to implement single and multiple input parameter perturbations an experimental setup was built.
It was possible to show that the single input modulation does not change the time-average output, in case of inlet concentration, or results in detrimental output, in case of total flow perturbation. For the simultaneous modulation of inlet concentration and total flow, the phase difference between the two inlets is the essential parameter to obtain beneficial operating conditions, in comparison to the steady-state. This is presented in Figure 2 and the corresponding inlet modulating function in Figure 3. A clear maximum is observed at the optimal phase difference.
![Figure 2: Experimental and simulative representation of simultaneous variation of the inlet concentration and volumetric flow rate for the hydrolysis of acetic anhydride with fixed amplitudes and varying phase shift.[Felischak, M., Kaps, L., Hamel, C., Nikolic, D., Petkovska, M., & Seidel-Morgenstern, A. (2021). Analysis and experimental demonstration of forced periodic operation of an adiabatic stirred tank reactor: Simultaneous modulation of inlet concentration and total flow-rate. Chemical Engineering Journal, 128197.]](/3548671/original-1636969253.jpg?t=eyJ3aWR0aCI6MjQ2LCJvYmpfaWQiOjM1NDg2NzF9--bbfe24945a7460de84d8267d38e8dd4de166e7ef)
[Felischak, M., Kaps, L., Hamel, C., Nikolic, D., Petkovska, M., & Seidel-Morgenstern, A. (2021). Analysis and experimental demonstration of forced periodic operation of an adiabatic stirred tank reactor: Simultaneous modulation of inlet concentration and total flow-rate. Chemical Engineering Journal, 128197.]
Based on these highly promising and worldwide first performed experiments the NFR method is applied to the industrially relevant methanol synthesis. This heterogeneously catalyzed reaction is performed at pressures of 30-60 bar and 230-260 °C adding to the complexity of implementing forced dynamic operation (Figure 3).
![Figure 3: Reaction network for the methanol synthesis for simultaneous feed of carbon monoxide and carbon dioxide.[Seidel, C., Jörke, A., Vollbrecht, B., Seidel-Morgenstern, A., & Kienle, A. (2018): Kinetic modeling of methanol synthesis from renewable resources. Chemical Engineering Science, 175, 130-138.]](/3548769/original-1636969253.jpg?t=eyJ3aWR0aCI6MjQ2LCJvYmpfaWQiOjM1NDg3Njl9--153de051e4993609769fbbfa2007d4df707ab8c4)
[Seidel, C., Jörke, A., Vollbrecht, B., Seidel-Morgenstern, A., & Kienle, A. (2018): Kinetic modeling of methanol synthesis from renewable resources. Chemical Engineering Science, 175, 130-138.]
To realize this challenging process a modular experimental setup in a mini plant scale was assembled with a Berty-type reactor as the centerpiece for realizing ideal CSTR conditions within the reactive zone (Figure 4).
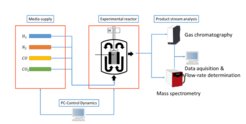
First results of the NFR method present interesting results to the optimized steady-state operation that are in good agreement with a rigorous optimization (Figure 5). Validation of the NFR results with rigorous numerical optimization for a minimal periodic time of 18 s.
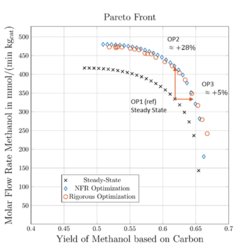
References
Felischak, M., Kaps, L., Hamel, C., Nikolic, D., Petovska, M., & Seidel-Morgenstern, A. (2021). Analysis and experimental demonstration of forced periodic operation of an adiabatic stirred tand reactor: Simulataneous modulation of inlet concentration and total flow-rate. Chemical Engineering Journal 410, 128197.
Nikolic, D., Seidel, C., Felischak, M., Milicic, T., Kienle, A., Seidel-Morgenstern, A., & Petkovska, M. (2022). Forced periodic operations of a chemical reactor for methanol systhesis - The search for the best scenario based on Nonlinear Frequency Response Method. Part II: Simultaneous modulation of two inputs. Chemical Engineering Science, 248 (Part A), 117133.
Leipold, J., Seidel, C., Nikolic, D., Seidel-Morgenstern, A., & Kienle, A. (2023). Optimization of methanol synthesis under forced periodic operation in isothermal fixed-bed reactors. Computers and Chemical Engineering 175, 108285.
Yevgenieva, Y., Zuyev, A., Benner, P., & Seidel-Morgenstern, A. (2024). Periodic Optimal Control of a Plug Flow Reactor Model aith an Isoperimetric Constraint. Journal of Optimization Theory and Applications, 202, 582-604.
Kortuz, W., Kaps, L., Leipold, J., Nikolic, D., Kinele, A., & Seidel-Morgentern, A. (2024). Experimental evaluation of forced periodic reactor operation for methanol synthesis, Poster at CHISA - 27th International Congress of Chemical and Progress Engineering, Aug 25-29, 2024, Prague, Czech Republic.
Seidel, C., Nikolić, D., Felischak, M., Petkovska, M., Seidel-Morgenstern, A., & Kienle, A. (2021). Optimization of methanol synthesis under forced periodic operation. Processes 9(5), 872.
Felischak, M., Kaps, L., Hamel, C., Nikolic, D., Petkovska, M., & Seidel-Morgenstern, A. (2021). Analysis and experimental demonstration of forced periodic operation of an adiabatic stirred tank reactor: Simultaneous modulation of inlet concentration and total flow-rate. Chemical Engineering Journal, 128197.
Nikolić, D., Seidel, C., Felischak, M., Miličić, T., Kienle, A., Seidel-Morgenstern, A., & Petkovska, M. (2021). Forced periodic operations of a chemical reactor for methanol synthesis – the search for the best scenario based on NFR method. Part I Single input modulations. Chemical Engineering Science, 248, 117134.
Nikolić, D., Seidel, C., Felischak, M., Miličić, T., Kienle, A., Seidel-Morgenstern, A., & Petkovska, M. (2021). Forced periodic operations of a chemical reactor for methanol synthesis – the search for the best scenario based on NFR method. Part II Simultaneous modulation of two inputs. Chemical Engineering Scince, 248, 117133.
Nikolić, D., Seidel-Morgenstern, A., & Petkovska, M. (2020). Nonlinear frequency response analysis of forced periodic operations with simultaneous modulation of two general waveform inputs with applications on adiabatic CSTR with square-wave modulations. Chemical Engineering Science, 226: 115842.
Seidel, C., Jörke, A., Vollbrecht, B., Seidel-Morgenstern, A., & Kienle, A. (2020). Corrigendum to “Kinetic modeling of methanol synthesis from renewable resources” (Chem. Eng. Sci. 175 (2018) 130-138). Chemical Engineering Science, 223: 115724.
Petkovska, M., Nikolić, D., & Seidel-Morgenstern, A. (2018). Nonlinear Frequency Response Method for Evaluating Forced Periodic Operations of Chemical Reactors. Israel Journal of Chemistry, 58(6-7), 663-681.
Reaction systems and process variants
Continuous production of antimalarial medicines
Artemisinin and its derivatives are currently the basis for the most effective medicines to cure malaria. In recent years, however, the high price for artemisinin as well as huge price fluctuations resulted in shortages of artemisinin-based therapies and gave rise for vast counterfeiting of the drugs. In order to make these medications more widely available the production process of artemisinin needs to be improved and innovated.
The main source of artemisinin is the extraction of the plant Artemisia annua, which contains only max. 1.4 wt-% of the target compound in the dried matter. Our approach to make the production process more cost-efficient is to increase the yield of artemisinin obtained from the extraction by utilizing dihydroartemisinic acid (DHAA) – the biological precursor to artemisinin. DHAA is contained in significant amounts in the plant and can be converted to additional artemisinin in a selective partial synthesis. Thus, an efficient production process for artemisinin can be achieved by coupling extraction with selective partial synthesis followed by an separation unit (Figure 6) for the final purification.
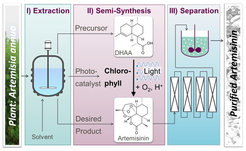
In the extraction step our research focuses on the simultaneous isolation of artemisinin and dihydroartemisinic acid from dried leaves by countercurrent solid-liquid extraction. The process is studied theoretically by a stage equilibrium cell model in order to predict and identify suitable operations condtions for the extraction. These conditions will be used for experimental investigation with a self-designed and custom built screw-extruder.
In the reaction step the DHAA obtained in extraction can be converted to artemisinin via a photooxidation followed by an acid-catalyzed reaction sequence (Figure 7). To initiate the photooxidation, a photoactive compound is required which transfers absorbed light energy to triplet oxygen forming highly reactive singlet oxygen. We showed that chlorophyll, a second byproduct of the extraction, can be utilized to initiate the photooxidation making the addition of other, often toxic photocatalysts unnecessary. Thus, artemisinin can be synthesized out of crude extract of A. annua by treating it just with oxygen, acid and visible light.
For the purification of artemisinin from reaction mixture without prior extraction, efficient combinations of chromatography and crystallization processes have been studied. 3-zone SMB chromatography with a capture step and seeded cooling crystallization were coupled successfully providing artemisinin at required purity constraints (>99.5%) and acceptable yield (Purity = 99.9%, Yield = 61.5%). Future work will be dedicated to adapt the developed methods to purify artemisinin from enriched extract.
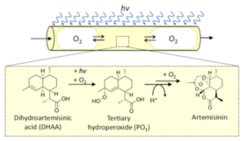
References
Triemer, S., Schulze, M., Wriedt, B., Schenkendorf, R., Ziegenbalg, D., Krewer, U., & Seidel-Morgenstern, A. (2021). Kinetic analysis of the partial synthesis of artemisinin: Photooxygenation to the intermediate hydroperoxide. Journal of Flow Chemistry. Journal of Flow Chemistry. 11, 641-659.
Horosanskaia, E., Triemer, S., Seidel-Morgenstern, A., & Lorenz, H. (2019). Purification of Artemisinin from the Product Solution of a Semisynthetic Reaction within a Single Crystallization Step. Organic Process Research & Development, 23, 2074-2079.
Münzberg, S., Vu, T. G., Seidel-Morgenstern, A. (2018). Generalizing Countercurrent Processes: Distillation and Beyond, Chemie Ingenieur Technik, 90 (11), 1769-1781.
Triemer, S., Gilmore, K., Vu, T.G., Seeberger, P.H., Seidel-Morgenstern, A. (2018). Literally Green Chemical Synthesis of Artemisinin from Plant Extracts, Angewandte Chemie International Edition, 57 (19), 5525-5528.
Horvath Z., Horosanskaia E., Lee J. W., Lorenz H., Gilmore K., Seeberger P.H., Seidel-Morgenstern, A. (2015). Recovery of artemisinin from a complex reaction mixture using continuous chromatography and crystallization, Organic Process Research & Development, 19 (6), 624-634.
Horvath, Z., O'Brien, A. G., Seeberger, P. H., Seidel-Morgenstern, A. (2014). Design and optimization of coupling a continuously operated reactor with simulated moving bed chromatography. Chemical Engineering Journal , 251, 355-370.
Gilmore K., Kopetzki, D., Lee J.W., Horváth Z., McQuade D.T., Seidel Morgenstern A., Seeberger P.H. (2014). Continuous synthesis of artemisinin-derived medicines, Chem. Comm, 50, 12652-12655.
Coupled enantioselective resolution and enzymatic racemization
Keywords: enantioselective HPLC, preferential crystallization, enzymatic racemization, mathematical modelling.
While significant improvement is made in enantioselective resolution techniques, such processes suffer a major drawback in their 50% yield constraint, as the unwanted by-product enantiomer is typically discarded after the separation. An attractive solution is the subsequent recycling of the by-product enantiomer by racemization. The racemization reaction converts the by-product into a racemic mixture of both enantiomers, which can be separated again, resulting in a significant yield increase.
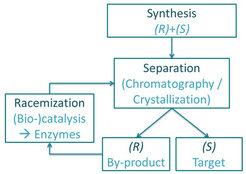
Racemization reaction
Racemization can be performed chemically, but this process often includes high temperatures, extreme pH values or is very slow. An eco-friendly alternative is the use of enzymes as biocatalyst, which not only accelerate the racemization reaction but in general also operate at moderate conditions, allowing an easier coupling with the resolution units.
Coupling options
In this group, model molecules are separated with enantioselective liquid chromatography (LC) and with preferential crystallization (PC) followed in both cases a by-product racemization with an immobilized racemase. The process with LC was studied for resolving the mandelic acid enantiomers using a mandelate racemase. For comparison, the coupled process with PC was tested for resolution of the enantiomers of the conglomerate forming amino acid asparagine coupled with an amino acid racemase catalyzed reaction. Suitable initial operating conditions for the process couplings were identified empirically for the single process units as well as for the coupled processes.
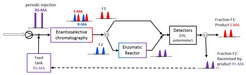
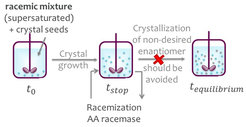
Enzyme immobilization
The enzyme production is often time consuming and can be expensive. Therefore, the enzyme is immobilized to enable reuse. Suitable immobilization procedures were developed for both enzymes. The amino acid racemase was purified with metal ion affinity chromatography and immobilized on Lifetech amino-activated resin. Due to its high activity, the crude extract of mandelate racemase was directly immobilized on Eupergit CM by Sigma-Aldrich.
Process simulation
Simulations based on mathematical models and experimental parameters were used for a deeper process understanding and to investigate the influence of operating conditions on the key performance indicators. In both cases the coupling not only increased the coupled process yield, but also its the purity and productivity. All obtained information were evaluated to find optimal conditions and to identify the potential of the two variants of the coupled process for resolution of enantiomers of other chiral compounds.
References
Harriehausen, I., Bollmann, J., Carneiro, T., Bettenbrock, K., & Seidel-Morgenstern, A. (2021). Characterization of an immobilized amino acid racemase for potential application in enantioselective chromatographic resolution processes, Catalysts, 11, 726.
Gänsch, J., Oliynyk, K., Potharaju, S., Seidel-Morgenstern, A., & Lorenz, H. (2024): Continuous chiral inversion by coupling enzymatic racemization with enantioselective fluidized bed crystallization. Industrial & Engineering Chemistry Research, 63, 18525-18535.
Bhandari, S., Carneiro, T., Lorenz, H., & Seidel-Morgenstern, A. (2022). Shortcut model for batch preferential crystallization coupled with racemization for conglomerate-forming chiral systems. Crystal Growth & Design, 22, 4094-4104.
Huskova, N., Gänsch, J., Mangold, M., Lorenz, H., & Seidel-Morgenstern, A. (2023). Improving results of a continuous fluidized bed process for the separaion of enantiomers by applying mathematical optimization. In A. Kokossis, M. C. Georgiadis, & E. Pistikopoulos (Eds.), 33rd European Symposium on Computer Aided Process Engineering, 52, 1391-1396.
Bhandari, S., Lorenz, H., & Seidel-Morgenstern, A. (2024). Shortcut model to evaluate the performance of continuous preferential crystallization for conglomerates forming chiral systems. Chemical Engineering Science, 299, 12539.
Harriehausen, I., Wrzosek, K., Lorenz, H., & Seidel-Morgenstern, A. (2020). Assessment of process configurations to combine enantioselective chromatography with enzymatic racemization. Adsorption, 26, 119-1213.
Carneiro, T., Wrzosek, K., Bettenbrock, K., Lorenz, H., & Seidel-Morgenstern, A. (2020). Immobilization of an amino acid racemase for application in crystallization‐based chiral resolutions of asparagine monohydrate. Engineering in Life Sciences, 20, 550-561.
Wrzosek, K., Harriehausen, I., & Seidel-Morgenstern, A. (2018). Combination of enantioselective preparative chromatography and racemization: Experimental demonstration and model-based process optimization. Organic Process Research &Development, 22(12), 1761-1771.